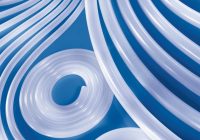
Stainless Steel and Single Use – More Similar than You Think…
- Posted by Howard Sneider
- On November 27, 2017
Over the past 20 years, the benefits and detriments of single use technologies for the manufacturing of biologics have been stated by proponents and detractors throughout the industry. Some issues are well defined (capital investment) while other topics lack clarity. This post will address a couple of often misunderstood facets of stainless steel and single use processes.
One of the hallmarks of single use processes is that they can provide a closed processing environment. However, this type of environment is not guaranteed; it must bear the same level of scrutiny and attention that a stainless steel process endures in order to assure a sterile or axenic environment. For instance, in a stainless environment, sterility is usually achieved by steam-in-place or autoclaving. Particular attention must be given to the path of steam flow, monitoring of sterile boundary temperature conditions, and prompt removal of condensate. Interconnecting piping must be sloped as required and also designed to ensure condensate removal. The procedure used to introduce and maintain the sterile environment must be performed according to the established tolerances.
In a single use environment, even though there is no steam flow, the connections must be designed to ensure compatibility (i.e., in materials and/or connection type), robustness, and quality assurance of the connection (where no other safeguards exist to prevent contamination). The same level of attention to performing procedures according to specification in a stainless steel environment must be maintained in the single use process. While the training required for single use and stainless steel may be different, proper training is critical to ensure that an effective, closed process is established and maintained.
One of the other qualities that is often espoused by single use processes is the amount of customization of single use assemblies. In actuality, the reason for the apparently greater customization of single use technologies has more to do with process design than with equipment or component capability. Legacy stainless steel facilities were designed using the methodology of designing a large dairy or chemical plant. Large reaction vessels and purpose-built piping were designed and installed for specific processes. Because the processing volumes required to satisfy the market demand were high, the vessels and equipment were large and, for the most part, immobile. On the other hand, single use facilities have always been designed as modules of smaller equipment because that is all that was available from the single use manufacturers. The smaller sized equipment and single use connection strategy favored reconfigurable plant designs.
In light of these arguments, it seems that customization is more a function of size than of material of construction. The industry is beginning to show examples of how the prevailing thoughts about material of construction and modularity are crossing over: large (~4000L), immobile, single-use buffer and bioreactor systems are becoming more prevalent and so are small, portable, reconfigurable stainless vessels used for high pressure applications, in particular, oligonucleotide synthesis .
The common thread between these two concepts is that design is the primary driver of the final process, whether it is based on stainless steel, single use, or a combination of systems. The best results from a particular design are always based on well-identified design constraints, design assumptions, and design loads. Achieving the optimal system and equipment design has the highest likelihood of success by focusing on the end-result product requirements.
0 Comments